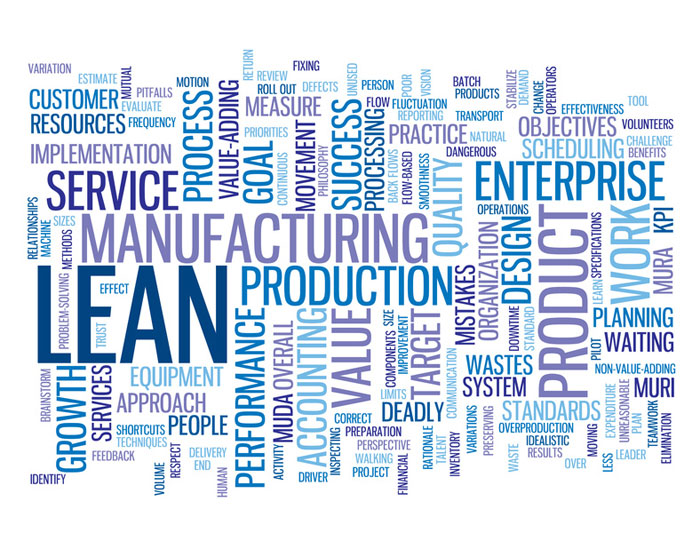
Apply lean methodologies to project management to gain a competitive advantage.
There’s no doubt that there is a vast amount of interest in lean principles. I’ve had multiple client requests – both ones who are interested in doing the latest and greatest program that they think might be the answer to “all their issues” and those who are interested in implementing culture change. I find that those clients who view lean as a culture change and are focused on long term fundamentals leapfrog the rest with bottom line results.
In today’s new normal business environment, sales are lackluster and resources are scarce yet customers expect more for less. Thus, the traditional avenues to success will no longer yield the same results. Instead, we must try new approaches and “think smart” to thrive in the new normal business environment. As project results can be a significant contributor to the bottom line, there is no better time to think about how to succeed in new ways. Why not incorporate the lean concepts that make sense to project management?
In my experience as a business consultant, a not-for-profit leader and a former VP of Operations, I’ve found that there are several lean principles which align with project management success. The top three include the following: 1) Focus on the customer. 2) Eliminate waste. 3) It’s all about the people.
- Focus on the customer: Similar to implementing lean in manufacturing environments, first take a step back and think about the customer. Who is the customer of your project? Or, said another way: who will benefit from the project?For example, one of my client projects is focused on reducing the past due metric. In this case, the customer connection is obvious – the fewer customer orders which are past due, the better service the customer will receive. Yet, even in this case, truly understanding what the customers’ value is important. Would the customers prefer a delivery date that is achievable and reliable or would they prefer a shorter lead time with less reliability? I’ve yet to work with a client who didn’t have customers who value different aspects of service higher than other customers. Find out and optimize based upon what each customer values.In another example, another client project is to implement an inventory management system. Who is the customer? There could be several: The end customer will likely receive better service with improved inventory accuracy. The CEO will likely improve profitability as the inventory management processes are optimized. The CFO will be much better equipped for a financial audit. And the list goes on. Although it is helpful to brainstorm all the benefits, it is vital to understand which is of value to your customer.
- Eliminate waste: There is a plethora of waste in project management. First, look for waste. Taking a step back, since it’s unlikely we’ll be looking for machine waste in project management, we should think about the best definition. I like the following – waste is that which doesn’t add value to the customer (and that which the customer is willing to pay for).It is interesting how often we become used to waste and don’t see it anymore. Thus, you need to put on a new pair of glasses to see the waste all around you. Can you accomplish the project in a fewer number of steps? Are you following up on every task or focusing attention on the critical path? What will provide a return on investment? Are you asking the project team for input and ideas to eliminate waste?
- It’s all about the people: Last but not least, those who succeed with lean initiatives understand that it’s all about the people. In essence, it is not an event; it is a culture change. Do you engage your people in the project? Do you ask for their input? Do you explain the project scope and its value to the organization? Do you do what you say you’ll do? I find this is much harder to do than it sounds yet it is a secret to unleashing your project talent. In my experience, an exceptional project team with a so-so project will beat a so-so project team with an excellent project every time!
Implementing lean for project management doesn’t require cash, capital or extra resources yet it can ensure that your project is delivered on time, on budget and with dramatic results. Although it is a good idea anytime, it is a must in today’s new normal business environment.
Published in “Project Times” website, October, 2011