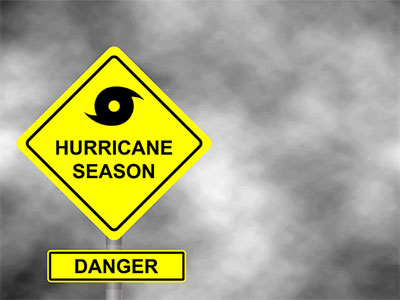
Supply Chain Disruptions: Hurricanes Wreak More Havoc
Hurricane Milton has blown through Florida. In addition to continuing havoc since it occurred close behind Hurricane Helene, it has created further supply chain disruptions that will have ripples throughout the globe. There are power issues at the Tampa port facility and manufacturers throughout the region shut down and are assessing damage. One potential widespread issue is related to the phosphate industry. Fertilizer producers were working to overcome production losses and power outages from Hurricane Helene during a critical time, and this will extend the recovery timeframe, impacting the agriculture and food production.
On the other side of the equation, to recover from these hurricanes, there will be significant rebuilding and construction, creating a spike in demand for related products. This will have a ripple effect throughout related industries, improving backlogs. On the other hand, it is also inflationary, thereby increasing costs, government spending, and interest rates down-the-line.
Common Sense Solutions
Companies should immediately implement common sense solutions if not done already. Certainly, backup plans, call trees, regional and government backed pre-planning, collaborating with your end-to-end supply chain and many other strategies should be deployed. Refer to our commentary in our recent interview with Inc. magazine’s article, “Hurricane Milton: How to Shore Up Supply Chains When Extreme Weather Events Become the New Normal“.
As a manufacturer or distributor, you should have emergency preparedness plans. A few topics that pop to mind include:
- Inventory: During hurricane season (or whatever weather or other disruptions likely in your region), the smart executives are approving bringing in excess inventory to cover for disruptions with suppliers, transportation issues, etc.
- Critical supplies: You should also ensure critical supplies are on hand or readily available. For example, if a generator is likely to be needed, don’t wait for an emergency to get one.
- Business continuation plans: Do you have backup plants, supplier agreements or other strategies in place to continue business during these turbulent times?
- Backup/ dual source suppliers: For your key materials, components, and ingredients, do you have a backup source of supply in a different region that you can count on?
- Systems/ technology infrastructure: Do you have redundant systems, backups and other strategies to ensure your ERP and related systems can come up quickly following an emergency? Do you have technical experts that will be available?
- Manual processes: Although it seems old school, manual business processes can save the day. Does your team know how to perform manual business processes?
- Emergency preparedness plans: Do you have communications plans and other blocking and tackling type plans available?
The good news is that most of these solutions are common sense. The bad news is that you cannot wait until the disruption occurs to react. Consider your most likely issues and the risks with the largest impact and prepare ahead of time.
Advanced Technologies & Predictive Planning Strategies
Beyond common sense, the best and brightest are pursuing advanced technologies and predictive planning strategies. In today’s global end-to-end supply chain, you are only as strong as your weakest link. Thus, you must not only be prepared for disruptions, but also roll out advanced technologies to use as tools to rapidly accommodate to changing circumstances.
For example, if you have advanced planning software integrated with your ERP system, as a disruption arises in your supply chain (supplier impacted by a hurricane, container ship impacted by Houthi rebels etc.), your system will recommend how to best avoid the issue, re-route and /or divert suppliers, reallocate production among sites, etc. It will not only address the issue, but it will evaluate the most cost effective solution so that you can maintain high levels of service while supporting profitable growth.
In addition, if you have a SIOP (Sales Inventory Operations Planning) process, you will continually be adjusting to changing circumstances in your customers’ supply chains and your suppliers’ supply chains. The process in combination with sales forecasting and predictive analytics software will keep a pulse on your demand plans by customer, regions, product lines etc. It will translate those plans into manufacturing and supply plans so that you can optimize your operational performance (greater efficiencies, lower waste, reduced costs), reallocate supply with changing conditions, and highlight key decisions such as expanding capacity in certain regions, increasing inventory in preparation for peak seasons, margin improvement opportunities of make vs buy etc.
For example, an electronics equipment manufacturer was dependent on a key supplier in a hurricane region and a key supplier in a high-risk region in Asia. The manufacturer purchased excess inventory prior to hurricane season, pre-planned storage solutions so that if/when a hurricane impacted their supplier or logistics suppliers, they could rely on inventory while weathering the storm. This strategy was built into their SIOP supply plans so that they could prepare their end-to-end supply chain for this cycle while maintaining reduced prices and secure supply. In addition, the SIOP process highlighted the risks associated with their dependency on the Asia supplier. Thus, they built a backup source of supply into their plans while pursuing additional suppliers and vertical integration possibilities in other low cost regions. Thus, they have been able to maintain high service levels with profitable growth. To learn more about how to roll out the process, read our book, SIOP: Creating Predictable Revenue and EBITDA Growth.
There are several additional strategies discussed in our eBook on how to craft tomorrow’s supply chain today. Download our complimentary special report, and please share your feedback and insights so that we can continue our predictive insights for thriving in this era of non-stop disruptions.
If you are interested in reading more on this topic:
Medical Supply Chain Optimization: The Solution to Non-Stop Disruptions