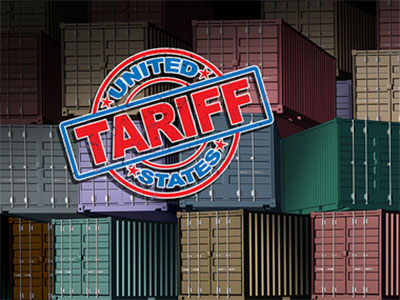
Volatility Abounds with Trade, Investments & Risks
The announcement of reciprocal tariffs has created extreme volatility in the stock markets and nervousness among executives. Geopolitical, supply chain, and cyber risks plague the end-to-end supply chain and have stimulated additional debates about control in the Panama Canal, Greenland, and global supply chains. What is the bottom line? VUCA (volatility, uncertainty, complexity, ambiguity) abounds in today’s supply chain, elevating the need for resiliency in the supply chain.
As Trump rolled out tariffs based on leveling the playing field to better align imports and exports (based on directionally correct formulas behind the tariffs), there will be inflationary pressures near-term while trade deals are negotiated and/or investments occur in the U.S. manufacturing base. Markets and businesses do not like volatility, and so they are down. On the other hand, now that the reciprocal tariffs are understood, executives can evaluate their supply chain networks and reconfigure, diversify, and expand manufacturing. Of course, these activities do not result in immediate changes with a snap of the finger, and so overall VUCA will remain intact during the transition / transformation.
Resiliency Will Be Paramount to Success
As companies navigate this VUCA-laden environment, resiliency will be paramount to success. The positive news is that most companies learned the value of creating resiliency during the pandemic. Prior to the pandemic, business was far more stable overall with fewer disruptions and fluctuations, and so although larger companies had backup plans, they were largely “in name only” when it came to bigger events. Post pandemic, companies have created additional backup plans and have been evaluating diversifying supply, reshoring, nearshoring, expanding manufacturing, and vertical integration in conjunction with modernizing and upgrading their ERP and related technology infrastructure. Thus, they are more prepared; however, generally, there is still concern about VUCA and how to ensure profitable growth.
The need for resiliency has been kicked into high gear with recent volatility such as the tariffs. For additional details related to strategies to address tariffs, refer to our recent interview and video with Authority Magazine. Taking it to the higher level, companies should focus on a few critical priorities:
- Strengthen capabilities: The best way to create resiliency is to create options. Cross-train so that you expand your Infrastructure, talent, technology, and other capabilities and have options to address whatever issue pops up next. For example, in 20 years of consulting, every client has a bottleneck of some sort in their end-to-end supply chain operations that constrains growth. It could be a supplier, a key machine, ERP functionality, a planner, etc. There is always a person /people tied to the bottleneck. In fact, in a few situations, we resolved significant past due orders and opened up substantial capacity for growth by simply hiring key skills ahead of the need and/or training critical resources to move to different bottlenecks. In another example, growth was limited by Engineering and Planning capacity, as the items could not be produced if they couldn’t be designed and planned. Therefore, they built increased capabilities into additional technical resources so that they could move resources to supplement and free up bottlenecks as needed to keep production flowing. Don’t wait for bottlenecks to arise. Upgrade processes, optimize the use of your ERP system, roll out advanced and/or emerging technologies, create back-up capabilities in your sites, etc.
- Gain forward-looking insights: It is impossible to drive if you are only looking in your rearview mirror. Develop forward-looking information and gain insights to drive critical decisions and know which capabilities to prioritize before the bottleneck occurs by rolling out SIOP (Sales Inventory Operations Planning) programs. SIOP will provide predictive insights into demand and supply and naturally highlight strategic decisions such as diversifying supply, insourcing vs outsourcing, supplementing capacity with offload resources, building inventory to bridge the gap during a transition, etc. The best SIOP programs include an upgrade of supply chain processes and technologies. For example, creating visibility in your end-to-end supply chain and predictive insights with advanced planning (APS) processes can be key to creating resiliency in handling disruptions while supporting customers. To learn more about how to successfully roll out SIOP, refer to our book, SIOP: Creating Predictable Revenue and EBITDA Growth.
Examples of Resiliency
As tariffs is the hot topic, it makes sense to talk through a few examples of resiliency or lack thereof that have arisen. An industrial manufacturer that supports the food industry had focused on ramping up a production facility in Mexico to support growth plans while maximizing margins. However, they have multiple facilities throughout the world and have focused on creating capabilities in all core facilities to scale up and/or to increase productivity. Thus, when the tariffs were announced, they were able to review SIOP charts showing revenue projections, capacity capabilities, and their ability to scale up/ down rapidly. They quickly developed backup plans to reallocate capacity to mitigate the impact of tariffs.
In another example, an industrial equipment manufacturer supporting the power industry saw significant growth potential coming down-the-pike. Thus, they invested in upgrading the use of their ERP system, rolled out a SIOP process, and developed additional manufacturing capabilities and sourcing options in the U.S. and Mexico. They developed relationships with short-term supply options while creating longer-term manufacturing capabilities and expanded their supply base. Thus, as disruptions like the tariffs occur (although the majority of products are more secure with the USMCA agreement), they have options to divert the sources of supply. They maintained their relationships to ensure backups were not “in name only”.
In a third example, an aerospace manufacturer built additional capabilities in their team. When everyone else cut staff to reduce costs, they found additional roles for their high-skilled resources to maintain robust talent capability. They also focused attention on building skills, cross-training, and rolling out additional manufacturing capabilities during this timeframe. Fast-forward a few years, and aerospace build plans were robust. The bottleneck across the supply chain was the ability to ramp up fast enough to fulfill orders. As other companies worked through inventory (stock programs) that covered the initial ramp up period but ran dry as stock was depleted, the aerospace manufacturer reallocated talent in their key facility to ramp up production capabilities. Thus, they were more successful than the competition in scaling up to meet the build plans as capacity flexibility went further than using inventory (once it was used, the capability was gone). They gained additional orders and contracts due to their resilience.
The Bottom Line
Navigating today’s VUCA-laden environment and preparing for the future with resilience is of paramount importance. Although it requires additional thought and focus, creating a resilient supply chain is largely uncommon common sense. In addition, building upon your organization’s intuitive and predictive capabilities and rolling out advanced and emerging technologies will be required to innovate and thrive in the next decade to come. Leaders that follow this strategy for success will have more opportunities than at any other time in history as Baby Boomers retire, supply chains are reconfigured for security, and the manufacturing renaissance stimulates growth.
If you are interested in reading more on this topic:
Supply Chain Transformation & SIOP Case Study for Success