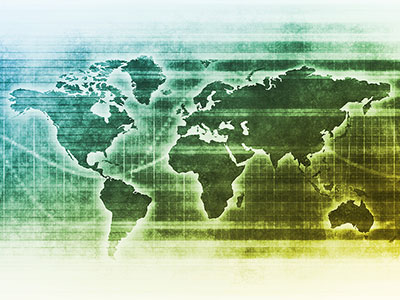
Supply chain optimization must remain a priority as disruptions continue. For example, although the Panama Canal started experiencing issues in the summer (refer to our article for details), it has been worsening lately. 40% of the goods movement from Northeast Asia to the U.S. East Coast go through the Panama Canal, and so the Panama Canal issues are driving shortages, late deliveries, and re-routing of goods.
Panama Canal Issues Worsen
Drought conditions are creating a new round of disruptions:
- Reduced container ships: by > 50% (from 40 to 32 earlier in 2023 to 25 Nov, 20 Jan & 18 Feb).
- Restrictions on ship draft: to a maximum ship draft to 44 feet (vs. 50 feet) – requiring larger ships to sail light or unload, rail across & reload
- Capacity restrictions: Neopanamax locks (handling larger ships) restricting to capacity by 50% (from 10 to 5 per day)
- Gas container ship impacts: LNG and VLGCs (very large gas carrier) will experience the greatest impact since deprioritized
Inflation impacts: Creating inflationary pressures, shortages and delays. Some ships paying up to $4M to go to the head of the line
The China Risk
In addition to the disruptions to the Panama Canal, there are other risks associated with the Panama Canal. Hutchison controls the terminals at both ends of the Panama Canal. Thus, if China wants to “control” the flow through the Panama Canal, they can do so via Hutchison. It is an important risk to consider.
Responses to the Panama Canal Issues
Proactive executives are not waiting to see how this turns out. They are pivoting. Several of the actions include the following:
- Alternate routes: Depending on the start and end point, companies are pursuing different routes. These include the Suez Canal and sailing around the southern tip of Africa or South America.
- Alternate modes of transportation: Depending on urgency, and start/ end points, companies are using air freight, rail etc.
- Alternate routes & modes of transportation: Companies are also going to an alternate U.S. port and sending product via rail or truck to its destination.
- Moving and/or reallocating manufacturing: Companies are certainly pursuing reshoring, nearshoring, and expanding manufacturing to minimize risks and shorten lead times. In addition, if they have multiple facilities and/or contract manufacturers, they are proactively moving manufacturing to support customer needs and mitigate risks.
- Forward position inventory: Depending on the manufacturing and distribution network, clients are also positioning inventory close to customers so that they can absorb additional disruptions without impacting customers.
- Change distribution network: Clients are also moving and expanding their distribution networks to better support customers. They are doing this in creative ways, sometimes partnering with customers, suppliers, and competitors.
The key is to proactively address these issues to mitigate the impacts to the customer and cost, and longer term, to revise your manufacturing and supply chain footprint and network to best support profitable growth and mitigate risk.
If you are interested in reading more on this topic:
Supply Chains are on the Move